Druckluft: Übersicht über Einsparoptionen
Auf einen Blick
Energieeffizienz
Handwerk / Industrie
Bundesweit
Beschreibung
In einigen Sektoren kann Druckluft für bis zu 20 % der gesamten verbrauchten elektrischen Energie verantwortlich sein ( in der Glasindustrie sogar bis zu 40 %). Im Durschnitt werden 7 % bis 11 % der elektrischen Energie eines Betriebes für Druckluft benötigt. Aufgrund des schlechten Wirkungsgrades ist Druckluft die teuerste Energieform in der Industrie.
Typische Anwendungsgebiete sind:
- Automatisierung: Zylinder, Motor, Ventile, Förderbänder, Webstuhl
- Aktivluft: Transport (z. B. Schüttguttransport)
- Prozessluft: Trocknen, Fermentieren, Belüftung von Absetzanlagen
- Vakuum: Verpackungen, Trocknung, Saugen, Hebevorrichtungen
Die größten Vorteile von Druckluft sind: Verfügbarkeit, Präzision, Skalierung, Sicherheit und geringes Gewicht der Werkzeuge.
Anwendungsgebiete nach Druck:
- Ultrahochdruck (> 40 bar): Dichtheitstests, Kraftwerke, Sauerstoffflaschen
- Hochdruck (17 bar – 40 bar): Rohrdrucktests, Blasformen von Kunststoffteilen
- Mitteldruck (10 bar – 17 bar): Schwerfahrzeuge, Spezialanfertigungen
- Niederdruck (< 10 bar): Die meisten industriellen Anwendungen liegen in diesem Bereich.
Die spezifische Leistung eines Verdichters liegt in der Praxis bei etwa 45 % oberhalb der theoretisch idealen Verdichtung.
Empfehlungen zur Optimierung
Es ist möglich, die Effizienz des Produktionsprozesses zu erhöhen, indem der Druckluftverbrauch und die Druckluftverluste durch die Optimierung der Verteilungskanäle und der angeschlossenen Komponenten reduziert werden. In vielen Systemen ist der Arbeitsdruck viel höher als nötig. Mehrere Studien haben gezeigt, dass das Druckniveau um bis zu 1 bar gesenkt werden kann, ohne die Produktivität zu beeinträchtigen. Durch die Senkung des für den ordnungsgemäßen Betrieb des Systems erforderlichen Drucks können kleinere Kompressoren eingesetzt und die Energieeffizienz des gesamten Systems erhöht werden.
- Auslegung von Antrieben: Häufig werden pneumatische Antriebe überdimensioniert und die Antriebskraft ist meist um ein Vielfaches größer als es in der Anwendung tatsächlich notwendig wäre. Dadurch brauchen diese Geräte dann größere bzw. leistungsstärkere Kompressoren, um auf den Soll Volumenstrom zu kommen. Fast die Hälfte aller Antriebe kann, wie Erfahrungen zeigen, eine Baugröße kleiner ausgelegt werden.
- Wartung: Bei mangelnder Wartung kann es aufgrund des inneren Verschleißes und tendenziell abnehmender Dichtheit zu einem Druckluft-Mehrverbrauch kommen. Pneumatische Anlagen, deren Verschleißteile regelmäßig überprüft und gewartet bzw. ausgetauscht werden, verursachen keinen höheren Druckluftverbrauch.
- Wechsel der Filterpatrone: Da Druckluft nicht zu 100 % frei von jeglichen Partikeln gemacht werden kann, benötigen Druckluftanwendungen in der Regel ein Filterelement. Oft werden die Filter zu spät gewechselt, weshalb ab einer gewissen Betriebszeit der Differenzdruck dieser Elemente sehr schnell ansteigt. In der Regel sollte ein Filter unbedingt einmal pro Jahr, jedoch spätestens bei einem Druckverlust von 0,35 bar gewechselt werden.
- Vermeidung offener Rohre für Blasanwendungen: Wenn bei industriellen Prozessen etwas abzublasen ist, wird häufig ein ganz gewöhnliches Rohr installiert, dessen Umfang von 2 bis zu 32 mm variieren kann. Das offene Rohr wird hierzu geformt und zurechtgebogen, um den gewünschten Blaswinkel und das erforderliche Blasmuster zu erhalten. Meistens funktionieren solche Installationen zwar, bringen aber Nachteile wie starke Turbulenzen, einen extrem hohen Energieverbrauch sowie potenzielle Gesundheitsgefährdungen mit sich. Im Allgemeinen können für die meisten Industrieanwendungen Druckluftdüsen, Sicherheitsblaspistolen und Sicherheitslärmdämpfer eingesetzt werden. Es gibt unterschiedlich effiziente Düsen hinsichtlich Blaskraft und Luftverbrauch oder z. B. Düsen mit der Fähigkeit, die die Düse umgebende Luft blaskraftverstärkend mitzunutzen.
- Geregelte Vakuum-Ejektoren: Vakuumejektoren wandeln nach dem Venturi-Prinzip Druckluft in einen Unterdruck um. Sie sind damit das Basis-Bauteil für jede Vakuumanwendung. In vielen Betrieben werden noch ungeregelte Vakuum-Ejektoren verwendet, welche ständig in Betrieb sind. Die ungeregelten Ejektoren sollten durch geregelte ersetzt werden. Geregelte Vakuum-Ejektoren arbeiten mit einer Luftsparautomatik und zeichnen sich durch sehr geringen Luftverbrauch aus.
- Einfach wirkende Zylinder: In vielen Anwendungen ist nur eine Bewegungsrichtung (z. B. der Ausfahrhub) des Zylinders zeitkritisch bzw. produktiv, während der Hub in die andere Bewegungsrichtung auch länger dauern kann und mit wenig Antriebskraft ausgeführt werden könnte. Trotzdem haben viele Verbraucher Zylinder verbaut, welche in beide Richtungen wirken. Die Verwendung eines einfach wirkenden Zylinders mit Federrückstellung spart den Druckluftverbrauch, welchen der Zylinder in der nicht-zeitkritischen Phase benötigt.
- Vermeidung von Totvolumen: Insbesondere in größeren Anlagen liegen oft hohe Distanzen zwischen Verbrauchern und Schaltanlagen. Dabei müssen die Schläuche bei jedem Schaltvorgang befüllt bzw. entleert werden. Unnötig lange Leitungen und Leerschaltungen sollen weitgehend vermieden werden. Dazu können Leitungen verkürzt bzw. die Verschaltung optimiert werden.
- Druckluftsubstituierung: Oft ist es aufgrund der gegebenen Bedingungen nicht nötig, Druckluft zu verwenden. Meist kann sie, bei gleichbleibender Produktivität, durch andere Technologien ersetzt werden. Zum Beispiel benötigt ein 6,5 kW Druckluftmotor einen Kompressor mit 132 kW, während man evtl. gleich einen 6,5 kW Elektromotor verwenden könnte.
- Weitere mögliche Substitutionen:
- Alternative elektrische Lösungen statt Druckluftkissen
- Druckluftlose Farbsprühanlagen, welche den Materialdruck zur Zerstäubung verwenden anstatt Druckluft
- Elektrische Vakuumerzeugung anstatt Venturi Prinzip
- Moderne, elektrische Schleifer
Bewertung von Optimierungen
Relevante technische Überlegungen | Elektrische Energie wird zu etwa 7 bis 20 % in Druckluftenergie (Volumenarbeit) umgewandelt. Die übrigen 80 bis 93 % werden in Wärme umgewandelt und landen entweder im Medium oder werden direkt an die Umgebung abgestrahlt. 50 bis 90 % dieser Wärme kann rückgewonnen werden, wovon 85 % in Wärmetauschern zurückgewonnen werden können. | ||
Wirtschaftlichkeit | Die Investitionen hängen von der Art des Eingriffs ab, der an der Anlage vorgenommen wird. Für den Austausch eines Kompressors beginnen die Kosten bei 3.000 – 4.000 EUR. | ||
Energieeinsparungen | Sektor | Anteil des gesamten Stromverbrauchs | Einsparpotenzial |
Handwerk, Handel, Dienstleistungen | bis zu 20 % | bis zu 50 % | |
Industrie | 7 – 20 % | bis zu 50 % | |
Wirtschaftliche Einsparungen | Minderwertige Technik austauschen: 15 % | ||
Reduktion von Komponenten: bis 15 % | |||
Auslegung von Antrieben: bis zu 40 % bezogen auf den Verbrauch des ursprünglichen Antriebs. | |||
Wartung: Je nach Größe der Leckage (1 mm ca. 150 Euro/Jahr) | |||
Wechsel der Filterpatrone: mehrere 1.000 Euro/Jahr | |||
Vermeidung offener Rohre für Blasanwendungen: > 10.000 Euro/Jahr | |||
Geregelte Vakuum-Ejektoren: mehrere 1.000 Euro/Jahr | |||
Einfach wirkende Zylinder: mehrere 1.000 Euro/Jahr | |||
Vermeidung von Totvolumen: 7 % Einsparung pro bar Druckabsenkung | |||
Durchschnittliche Amortisationszeit | 3 – 6 Jahre | ||
Emissionen | 0,702 kg CO2/kWhel (CO2-Ausstoß bei der Produktion von 1 NL/min Druckluft für eine Stunde) | ||
Vorteile für die Umwelt | Reduktion der CO2-Emissionen durch geringeren Energiebedarf | ||
Nicht-Energievorteile (Mehrfachnutzen) |
| ||
Replizierbarkeit | hoch |
Praxisbeispiel
Austausch von Komponenten (Österreich, 2011 – 2013)
Ausgangssituation
- hohe Leckagen
- großer Filterwechsel Intervalle
- offene Rohre für Blasanwendung
- keine Wärmerückgewinnung
Beschreibung der Optimierung
- Optimierung der Regelungsparameter bzw. Intervalle der Filteranlagen
- Leckagenbehebung
- Energiespardüsen einbauen
- konsequente Verbraucheroptimierung durchführen
- Wärmerückgewinnung nutzen (aus Abluft, Kesselhaus, Pumpenstationen)
Kosten der Implementierung: 108.000 EUR
Amortisation der Implementation: 3 Jahre
- OPTIMIERUNG_VON_DRUCKLUFTVERBRAUCHERN.pdfOptimierung von DruckluftverbrauchernGröße: 175 KB
Datum: 06.09.2024
Quellenangabe
Partner
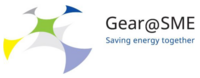
Gear@SME
Die Maßnahmenbeschreibung stammt vom Projekt GEAR@SME. Das Projekt lief von 2020 bis 2023 und wurde durch das Horizon-2020-Programm der Europäischen Union gefördert. Zu den 10 Projektpartnern gehört u.a. die Berliner Energieagentur.Website öffnen
Datum
Zuletzt geändert am 06. September 2024Verwandte Artikel
Beitrag von Max Ulrich, Meterologe und Inhaber von Atmovera, einem Beratungs- und Dienstleistungsunternehmen spezialisiert auf Klimarisiken (4.4.2024).
Strategien für Energieeffizienz bezeichnet die Nutzung von weniger Energie zur Erstellung einer Dienstleistung oder eines Produkts.
Zu hohe Lüftungsraten sind ohne Messgeräte nicht festzustellen
In einem Gewerbegebiet teilen sich viele Unternehmen eine gemeinsame Infrastruktur, konzentrieren Lärmemissionen auf einen beschränkten Raum und minimieren den Flächenverbrauch.
Wärmepumpen in Gewerbe und Industrie: Energieeffizienz steigern und Förderungen nutzen.